Processing Materials
High frequency induction melting furnaces have good combustion effects on stainless steel, high chromium, high manganese steel, electric heating alloys, intermediate alloys, pure metals (Ni, Co, Cu, etc.), ferroalloys such as ferrosilicon and ferrochrome, ores, slag, sintered ores, oil shale, graphite, tungsten carbide, rare earth materials, and various non-metallic raw materials.
Application scope
The frequency of the power supply used is above 10000Hz, with a maximum of 1MHz. High frequency induction furnaces require frequency conversion equipment. The capacity of high-frequency induction melting furnace is generally below 100kg due to the limitation of power supply. High frequency induction furnaces are mainly used for scientific research in laboratories. High frequency power equipment can be equipped with quenching equipment for surface quenching of mechanical parts in the heat treatment department.
Advantages and characteristics
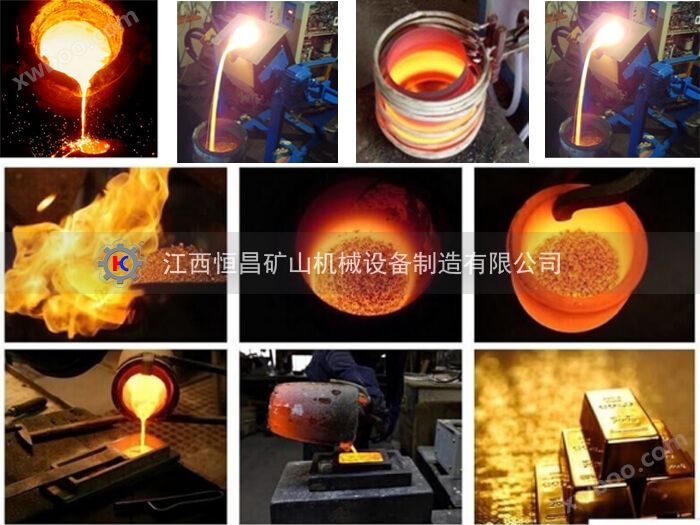
1. The high-frequency induction melting furnace adopts advanced MOSFET and IGBT technology to achieve automatic frequency tracking;
2. Fully functional, if any parameter of overcurrent, overvoltage, overheating, water shortage, or phase loss fails to meet the requirements, the machine will automatically protect itself;
3. High frequency induction melting furnace equipment has fast melting speed, energy saving and environmental protection.
product mix
The high-frequency induction furnace has a high melting rate and can maintain power operation at the optimal frequency band during the melting process, greatly eliminating the adverse effects of new lining on the melting speed; High quality molten steel and high yield of castings; High power factor, during the operation of the whole machine, the power factor can reach over 97%, and it will not interfere with the power grid.
High frequency high current flows towards a heating coil that is wound into a ring or other shape (usually made of copper tube). As a result, a strong magnetic beam with instantaneous polarity change is generated within the coil. When a metal or other heated object is placed within the coil, the magnetic beam will penetrate the entire heated object. In the opposite direction of the heating current inside the heated object, a corresponding large eddy current will be generated. Due to the presence of resistance within the heated object, a significant amount of Joule heat is generated, causing the object's temperature to rapidly rise. To achieve the goal of heating all metal materials.

Technical Parameter
model |
JL-15KW |
JL-25KW |
capacity |
1-2KG gold/silver/copper |
3-5KG gold/silver/copper |
Melting speed |
3-5 minutes/furnace |
3-5 minutes/furnace |
INPUT VOLTAGE |
Single phase 220V |
3-phase 380V |
Maximum oscillation power |
15KW |
25KW |
Maximum input current |
37A |
24A |
Frequency |
30-100KHZ |
30-100KHZ |
Cooling water requirements |
>0.2MPa, 2-6L/Min, ≤40℃ |
>0.2MPa, 2-6L/Min, ≤40℃ |
Duty cycle |
100% |
100% |
size |
500*210*460mm |
550*240*480mm |
net weight |
21kg |
28kg |